Background
Since 2000 I have religiously recorded our energy usage every week. I also have an external temperature sensor so I can monitor the weather. In 2008 we replaced an old (22kW) cast iron boiler with a Viessmann 18kW condensing heat only boiler. We had a smart meter installed in 2020 making the collection of energy usage data easier and with much better time resolution, and in September last year I attached temperature sensors and data logging to our hot water tank and boiler flow.
For the last three years I have been operating our boiler at a flow temperature of just 50°C to see how well our house would cope with a heat pump (or smaller gas boiler).
The following are my thoughts based on an examination of this data.
Firstly remember that a wet central heating system is in fact four interlinked control systems.
- The boiler (or heat pump) provides energy to the circulating water.
- The circulating water is controlled by balancing valves, zone valves and thermostatic valves to the radiators.
- The radiators give up their energy to the rooms
- The rooms leak the heat energy to adjacent rooms and ambient.
In some respects it is surprising that the system works! The whole system is a balancing act between heat supplied by the boiler, distributed to the radiators, transferred to the rooms and finally lost to ambient.
Heating States
When you consider the heating system it can be in one of five states.
- Off
Not very interesting!
- Demand exceeds boiler minimum power output
The boiler ignites (ours starts at the high burner rating). Energy is supplied heating the circulating water a proportion of which is lost by the radiators. Excess energy causes the circulating water to heat up, more energy is lost from the radiators, and so the system heats up. The boiler may well be operating at its highest rating whilst the circulating water reaches it’s (boiler) set-point. Bigger boiler, the faster this will occur.
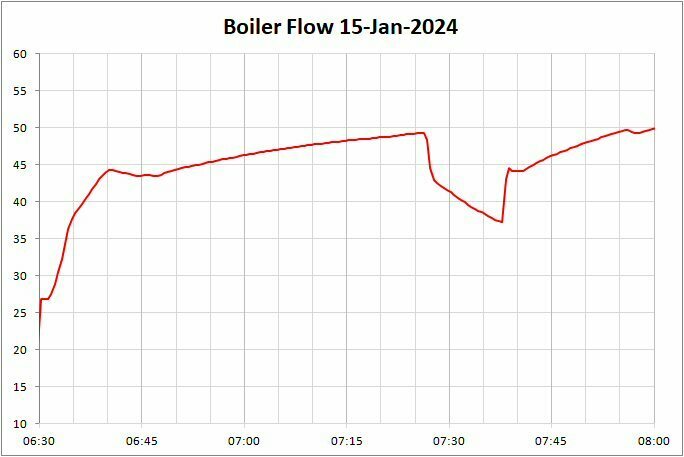
However heating up the circulating water takes surprising little time. Our 18kW boiler takes just 5 minutes before it starts to throttle back, and just a further 5 minutes before it has modulated down to its lowest firing rate (7kW). The flow temperature now slowly increases until at 07:25 the flow temperature exceeds the set-point and the boiler turns off.
Some things to note from this:
- A 36kW boiler would be throttling down after just a few minutes.
- The speed at which rooms heat up is determined by the temperature and size of the radiators and not the power of the boiler.
- Minimum Boiler Output Exceeds demand
At 07:25 the minimum output from the boiler exceeds the demand and the flow temperature exceed the set-point (50°C). The only option now is for the boiler to turn off.
The boiler must now either wait some time, or wait for the flow temperature to fall below some lower value before turning back on. Our boiler seems to wait until the flow temperature has fallen around 13°C to 15°C below the set-point, before turning back on.
In this example this takes around 11 minutes. The boiler re-ignites at the high fire rate, but within 30 seconds modulates down to the lowest rate. After a further 20 minutes the set-point is reached and the boiler turns off and the cycle repeats.
Some things to note:
- The average flow temperature has now REDUCED (11 minutes off, 20 minutes on). It averages around 45°C not the 50°C set-point.
- Because the flow temperature has fallen the dwelling will heat more slowly
- A larger boiler would result in less time heating, more time cooling, and hence an even lower average flow temperature.
- A smaller boiler would have been able to maintain the 50°C set-point for longer allowing the rooms to heat quicker!
- So YES, a smaller boiler can result in your house heating up faster!
- Thermostatic Control
Stages 2) and 3) above generally occur when the thermostat is calling for heat (room temperature not satisfied).
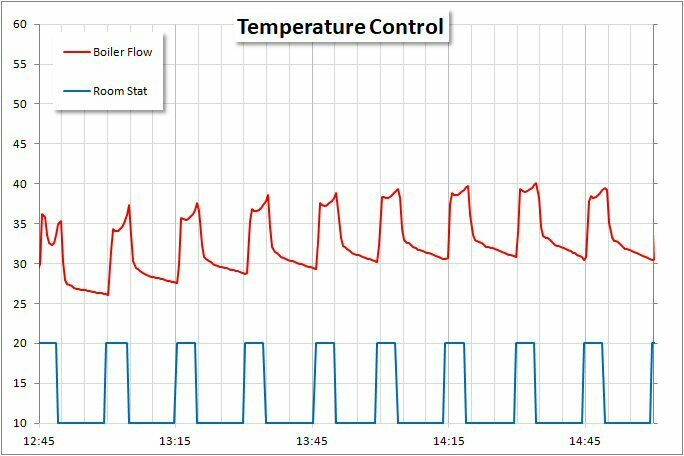
As the house approaches temperature the thermostat will start to come into play. Our Danfoss thermostat (in the hall) utilises TPI (Time, Proportional and Integral) and varies the on and off times to provide for better temperature control with minimal overshoot. Our Danfoss appears to have a period of around 15 minutes.
Other control schemes, such as those using Opentherm or Weather Compensation may instruct the boiler to adjust the flow temperature.
Again you can see the boiler lights at its high rate and quickly modulates down to its minimum firing rate. Before the flow temperature reaches the boiler setpoint the thermostat turns the boiler off. Here the average flow temperature rises from around 29°C to 33°C over the 2 hour period.
- Boiler “Short Cycling”
As I mentioned at the start there are a lot of devices all vying for control of the system. As the house as a whole heats up thermostatic valves around the house will start to throttle back the flow to their radiators. The consequence of this is that the flow rate of the circulating water starts to fall.
Looking at four extremes:-
- Boiler input 7kW, Flow Rate 20l/min, Temperature rise 5°C
- Boiler input 7kW, Flow Rate 9l/min, Temperature rise 11°C
- Boiler input 18kW, Flow rate 20l/min, Temperature rise 13°C
- Boiler input 18kW, Flow Rate 9l/min, Temperature rise 21°C
So when the flow rate is high and the boiler ignites at its high rate it should be able to throttle back before the flow through the boiler exceeds the set-point.
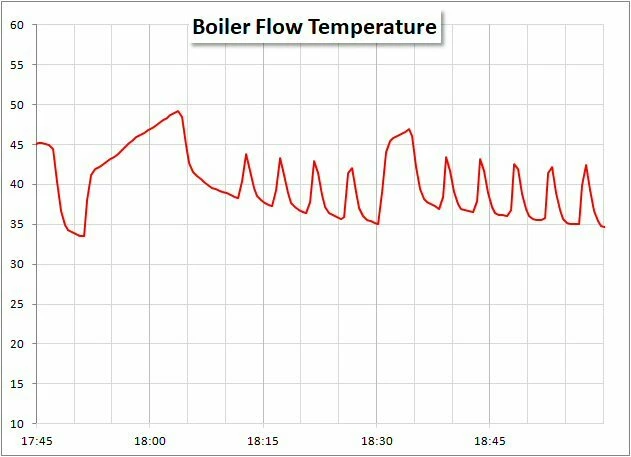
However when the flow rate is low it may not be able to throttle back fast enough, the flow temperature will exceeds the boiler set-point and it will turns off.
This problem tends to occur on milder days when the load is low and many radiators have been closed off by their TRVs.
The boiler turns on at around 17:50. Within a minute the boiler has started to throttle back and we lose the steeply rising temperature to make way for a more gradual rise. AT 18:05 the set-point is reached and the boiler turns off. At around 18:10 the boiler turns back on. Within 30 seconds the outlet from the boiler exceeds the set-point and it turns back off again. The short heating spike is actually too short for the temperature sensors (which are clamped onto the pipe work) to follow. This process repeats a further three times (every five minutes) before the boiler manages to reduce down enough for the boiler to remain on. Even at the lower power the set-point is again reached and this time we have five attempts before the boiler can operate continuously.
This places a significant demand on the boiler.
The only way I could think of to cure this problem was to increase the minimum flow rate. I ended up increasing the head on the pump and opening up the balancing valves on two small radiators which did not have TRVs (utility and toilet).
Discussion
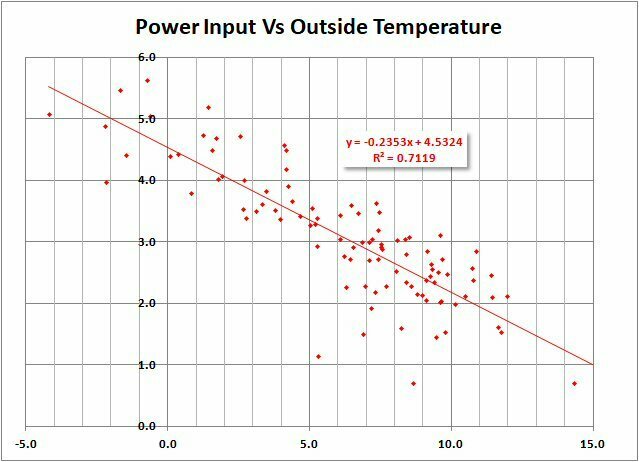
What seems to be most important is that the low fire rate should match the typical winter demand. In my case this would be around 2.5kW (where most of the points lie). This should mean that the heat source should be able to modulate down and provide steady input to the system (rather than pulsing on and off every 15 minutes or so).
Secondly the maximum rate should be sufficient for coldest (likely) days. So 5.5kW should be OK, or 7kW to allow for exceptional days and water heating.
A more powerful system would result in little benefit (possibly shaving mere minutes of the warm-up time of the house), but potentially causing the house to heat slower and suffer from “Short Cycling”.
Many (many!) years ago I visited Watson House, one of five British Gas research centres, dedicated to improving domestic utilisation. On my tour we had a brief presentation on heating “comfort”. One recommendation was to reduce draughts and fit carpets (to keep your feet warm). Another was that we notice changes in temperature, so a room that is steady at say 19°C will feel more comfortable than a room that cycles between say 19°C and 20°C. You notice the room cooling.
Weather Compensation (WC) systems should be more comfortable. They are using “feed forward” to estimate the required flow temperature based on the outside temperature. By contrast a conventional thermostat must detect a difference from a set point and then raise or lower the flow temperature to compensate. A WC system anticipates what is required; a standard thermostat is always playing catch-up.
Why would a WC system not work?
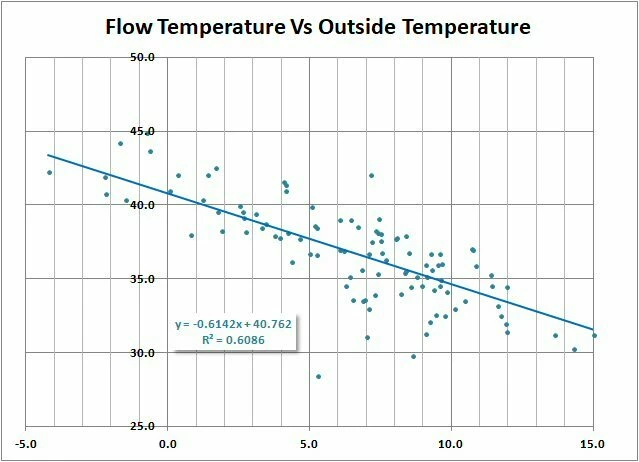
If I were to fit a WC system to my existing boiler then on a mildish winter’s day, say between 5°C and 10°C, I would be looking at a flow temperature of say 37°C. But my boiler has a 13°C hysteresis so how will it achieve the average flow temperature required? Does it set the boiler set-point to 37°C? But when it reaches the set-point it will turn off and wait for the flow to cool to 24°C!
Does it use a boiler set-point of say 50°C and then switch the boiler on and off to achieve the 37°C average?
Sorry I don’t know how it manages it!
But it might explain why WC systems may not work well on conventional systems (I’m thinking combi boilers which tend to be larger for the instantaneous water demand)
… And Finally some thoughts on radiator sizing and thermostat placement.
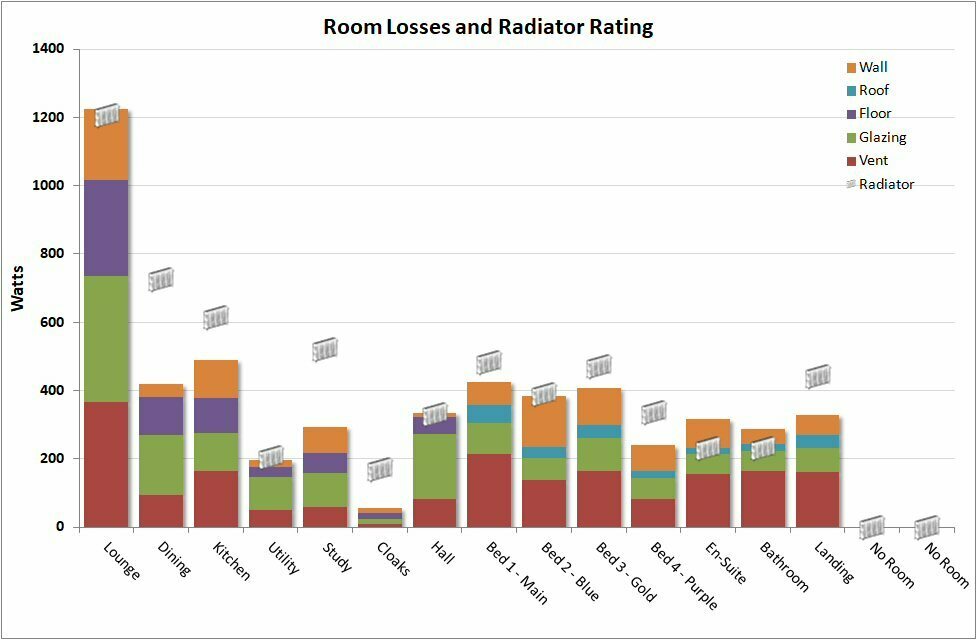
There is lots of discussion about sizing radiators to suit the lower flow temperatures that benefit heat pumps (and gas boilers).
What you might also consider is that if the thermostat controlling the heating system is in a room with an over-sized radiator then it may be difficult to achieve the required temperatures in some of the other rooms. So if the thermostat was in my study then several of the rooms may not have reached temperature when the study cuts back the heating.